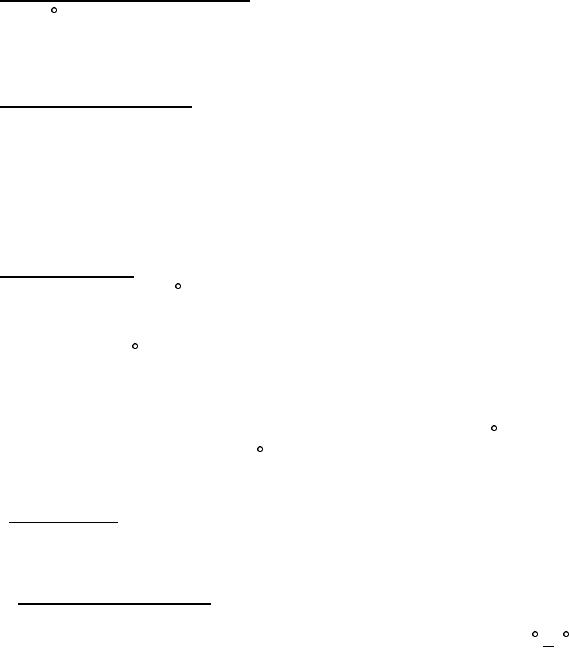
MIL-PRF-25676E
b. The adapter and nozzle shall then be connected, and a hydrostatic pressure of 500 psi
using a lubrication oil be applied at the adapter inlet for 1 minute. There shall be no visible
signs of leakage.
c. The adapter shall again be subjected to the pressure tests of 4.5.4 (b), (c), (d) and (e).
4.5.6 High temperature and leakage test. A high temperature test shall be made at a
temperature of 275 F. The adapter shall be heat soaked for 2 hours while maintaining this
temperature. The pressure tests of 4.5.4 (b), (c) , (d) and (e) shall again be applied. There
shall be no visible signs of leakage.
4.5.7 Vibration and leakage test. The adapter shall be mounted to a representative
section of aircraft structure and subjected to a vibration test. A hydraulic back pressure
equivalent to a 2 foot head of oil shall be maintained in the adapter during the test period. The
protective cap shall be installed on the adapter during one-half of the total test period.
Following the vibration period, the leakage tests of 4.5.4 shall be repeated. At no time during
the test shall the protective cap become loosened or unattached, nor shall there be any visible
signs of leakage.
4.5.8 Pressure drop test. With the adapter connected to a nozzle, the assembly shall be
filled with oil and cold soaked at -65 F ambient air temperature for 24 hours. While
maintained at this temperature, the following procedure shall be conducted:
a. Lubricating Oil at -65 shall be flowed through the assembly at a rate of 1 gpm. The
maximum pressure drop across the assembly required to establish rated flow shall be
determined.
b. The pressure drop shall then be with the oil entering the assembly at -45 F and at a
flow rate of 1 gpm. The pressure drop with -45 F oil shall not exceed that shown on
MS24476.
4. 5. 9 Measurements. Pressure measurements shall be taken at least 10 diameters
upstream and 10 diameters downstream from the assembly. Temperature measurements shall
be taken 10 diameters upstream of the assembly.
4. 5. 10 Accelerated corrosion test. The adapter shall be immersed in a solution
consisting of 2.5 percent, by weight, of sodium chloride in distilled water. After immersion,
the solution shall be drained and the adapter heated in an oven to a temperature of 130 +5
for a period of not less than 1 hour. The immersion and heating cycle shall be repeated 50
times. The adapter shall not be operated at any time during these cycles. Immediately after
completing the immersion and heating cycles, the adapter shall be thoroughly washed with
warm water to remove all salt accumulations. The adapter shall then be dried, wetted with oil,
and connected for three complete cycles. There shall be no corrosion of any part to a degree
which might adversely affect the performance of the adapter.
6
For Parts Inquires call Parts Hangar, Inc (727) 493-0744
© Copyright 2015 Integrated Publishing, Inc.
A Service Disabled Veteran Owned Small Business